Temperature control of plastic pelletizing extruder
In today’s society, the use of plastic pelletizing extruder is becoming more and more widespread, and many plastic recycling manufacturers make recycled plastic pellets for high profits.
However, many people have questions about how plastic pelletizing extruder work and temperature control, especially regarding the need for heating. This article will detail the working principle of plastic granulators and why they need heating, and emphasize the importance of temperature in an extrusion pelletizing machine.
Why does plastic pelletizing extruder need to be heated?
Plastic pelletizing extruder is a kind of equipment that can recycle waste plastics by heating and extruding them, melting them and making them into granules again, which can be used to produce various plastic products.
The heating temperature of the plastic pelletizing extruder needs to be precise, and the staff has to ensure the accuracy of the temperature in each temperature zone of the machine. Different types of plastic raw materials have different melting points, so the plastic pelletizer requires a high degree of temperature accuracy during production, and the temperature set for different raw materials varies.
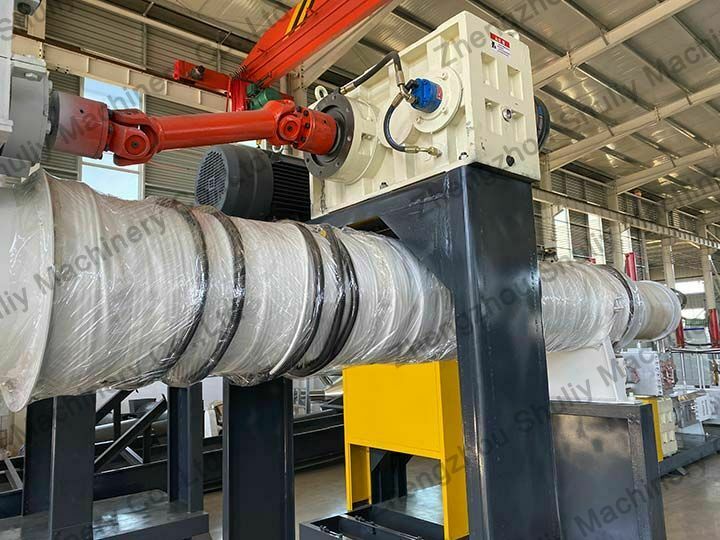
Many plastic products require temperature control within a range of ±5°C, otherwise scrap or defective products may result. To achieve accurate temperature control, many models of plastic pelletizers use air or water cooling systems for temperature reduction control. Through a combination of heating and cooling regulations, the plastic pelletizing extruder is able to precisely control the temperature to ensure the quality and performance of the final product.
Importance of temperature for plastic pelletizing extruder
The extrusion pelletizing machine requires a certain amount of heat during the pelletizing process. Temperature plays a key role in the melting, extrusion and pellet formation of plastics. The right temperature can bring the plastic material to the right molten state, improve the plastic flow and extrusion performance, and ensure the shape and quality of the pellets.
If the temperature is too low, the plastic may not be completely melted, resulting in a decrease in the quality of the pellet; if the temperature is too high, the plastic may decompose, oxidize or change color and other adverse reactions, affecting the quality of the final product. Therefore, reasonable temperature control is the key to the work of an extrusion pelletizing machine.
In addition to the accuracy of temperature control, the work of extrusion pelletizing machine also requires reasonable temperature configuration. Usually, a plastic granulator consists of several temperature zones, each of which can be adjusted independently. This is because different plastic materials have different temperature requirements in the melting and extrusion process. By reasonably configuring the temperature of the temperature zones, the processing requirements of different plastic materials can be met and the quality and performance of the final product can be guaranteed.