Basic structure of plastic granulation equipment
By understanding the components and functions of plastic granulation equipment, plastic granules manufacturers and operators can effectively utilize this equipment to produce high-quality plastic pellets for various applications.
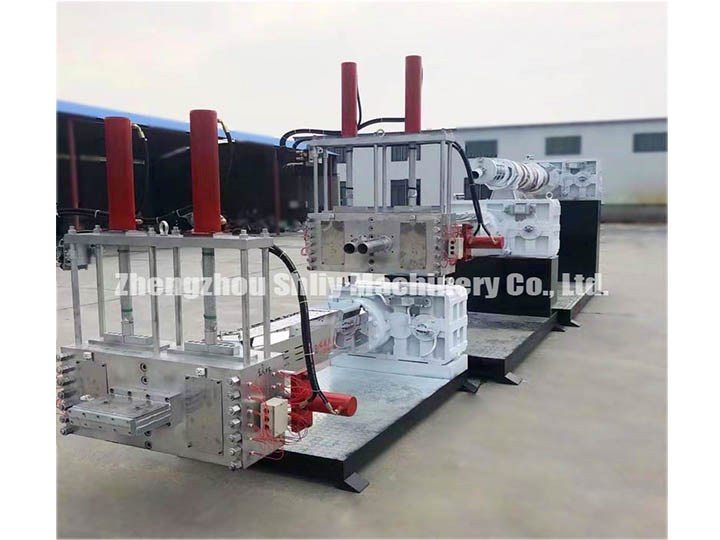
Extrusion system of plastic granulation equipment
The extrusion system is a crucial component of the plastic granulation equipment. It consists of the screw, barrel, hopper, die head, and mold. The plastic material undergoes plasticization within the extrusion system, transforming into a uniform melt. Under pressure, the screw continuously extrudes the molten plastic through the die head.
Plastic granulation equipment’s screw
The screw is a vital part of the plastic granulator machine for sale, significantly influencing its application range and production efficiency. Made of high-strength and corrosion-resistant alloy steel, the screw undergoes various processes, such as tempering, nitriding, and chrome plating. Different screw designs are employed based on the specific characteristics of the plastic being processed.
Barrel of waste plastic extrusion machine
The barrel is a metal seamless tube typically made of alloy steel with high heat resistance, pressure resistance, durability, and corrosion resistance. It works in conjunction with the screw to achieve tasks such as plastic crushing, melting, fusion, plasticization, venting, and compaction.
The barrel of plastic granulation equipment ensures the continuous and uniform delivery of plastic to the forming system. Generally, the length of the barrel is 18 times its diameter, ensuring thorough heating and plasticization of the plastic material.
Die head of waste plastic extrusion machine
The die head consists of an alloy steel inner sleeve and a carbon steel outer sleeve. It houses the forming mold. The die head’s role is to convert the rotating plastic melt into a parallel linear motion, uniformly and smoothly guiding it into the mold while imparting the necessary molding pressure.
The plastic melt, plasticized and compacted in the barrel, flows through the die head neck via a porous filter plate and enters the die head forming mold. The mold core and mold cavity are properly matched, creating a continuously dense cylindrical layer with a decreasing cross-sectional area around the core.
Transmission System of plastic granulation equipment
The transmission system of plastic granulator machine for sale is responsible for driving the screw and supplying the necessary torque and speed during the extrusion process. It typically consists of an electric motor, gearbox, and bearings.
The cooling system ensures that the plastic remains within the desired temperature range during the extrusion process. It eliminates excess heat generated by shear friction during the rotation of the screw, preventing excessive temperatures that can cause plastic decomposition, scorching, or difficulties in shaping. The barrel cooling can be achieved through water or air cooling.
Small and medium-sized plastic granulator machine for sale often use air cooling, while larger machines employ water cooling or a combination of both. The screw cooling mainly employs central water cooling to increase solid conveying capacity, stabilize extrusion output, and improve product quality. Cooling at the hopper serves two purposes: enhancing the conveying action on adhered materials and ensuring the normal operation of the transmission system.
Shuliy Machinery plastic granulator machine for sale has shipped to many countries like Saudi Arabia, Congo, Ethiopia, Negeria and so on. If interested, welcome to consult us any time!