How a Plastic Runner Crusher Can Help Injection Molding Factories Recycle Waste Efficiently
In every injection molding factory, runners, sprues, and gate scraps are inevitable by-products of daily production. These leftover materials are often hard, irregular, and bulky—taking up valuable space and increasing disposal costs. But what if you could turn this “waste” into valuable recycled material? That’s where a plastic runner crusher becomes essential.
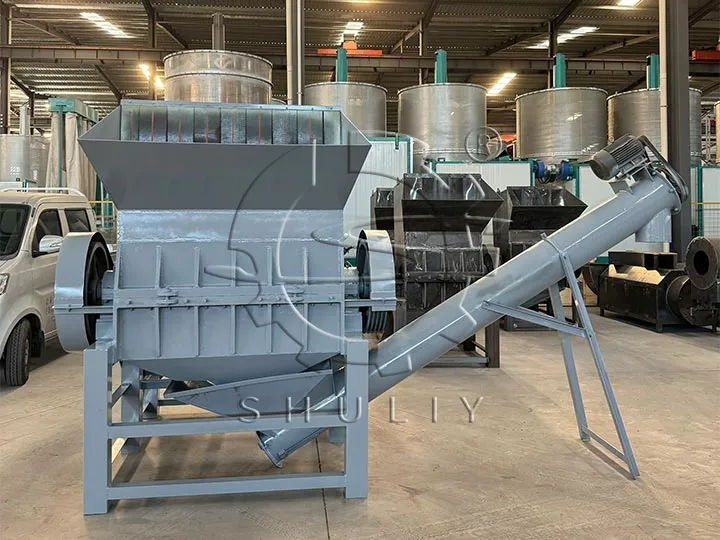
What Are Plastic Runners?
In injection molding, runners refer to the solidified plastic channels that deliver molten resin into the mold cavities. After molding, these runners are separated from the finished products, along with sprues, gates, and sometimes overflow flash. Instead of discarding them, many factories are now choosing to crush and recycle them back into production.
Why You Need a Plastic Size Reduction Shredder
A plastic size reduction shredder is designed to break down these hard plastic leftovers into small, uniform flakes—typically 10–40 mm in size. This makes them suitable for regrinding, re-pelletizing, or even direct reuse in new molding batches.
Using a runner crusher helps factories:
- Reduce plastic waste
- Lower raw material costs
- Create a closed-loop recycling system
- Save storage and transport space
What Materials Can Be Processed?
Our plastic runner crushers are capable of handling:
- Rigid sprues and gates (PP, PE, ABS, PA, PC)
- Overflow flash and trimming scrap
- Mixed scrap from multi-cavity molds
- Cold slugs and rejected parts
These shredders are built with strong motors (5.5kW–15kW) and wear-resistant blades to ensure continuous operation and consistent output.
From Crusher to Granulator
Once shredded, the plastic flakes can be:
- Directly reintroduced into injection molding machines
- Sent to a plastic granulator for further process: pelletizing
- Fed into an extrusion pelletizing line to produce recycled pellets
Conclusion: A Smart Investment for Injection Molders
Investing in a plastic runner crusher is a smart move for any injection molding facility looking to reduce waste, save money, and operate more sustainably. With a high-performance plastic size reduction shredder, your factory can turn daily by-products into valuable resources—efficiently and cost-effectively.