How are plastic products made?
Plastic is now ubiquitous in our lives, from keyboards, mobile phone cases, pens in your hands, shopping bags to small fans, buckets, washbasins, etc, but have you ever wondered what their process is like?
The production of plastic is mainly divided into three stages: preparation before molding, injection molding process, and post-processing of plastic parts.
Preparation before molding
1. Plastic is made from petroleum;
2. Transport the extracted crude oil to a petroleum processing plant for dehydration and desalination.
3. Distillation then produces various fuel oils, such as gasoline, kerosene, diesel, etc.
4. The raw material for plastics is a kind of cracking process called petroleum.
5. The raw material gases such as ethylene and propylene are prepared first and then subjected to addition polymerization to produce materials such as polyethylene and polypropylene, also called resins.
6. Heat-processed into polyethylene plastic and polypropylene plastic.
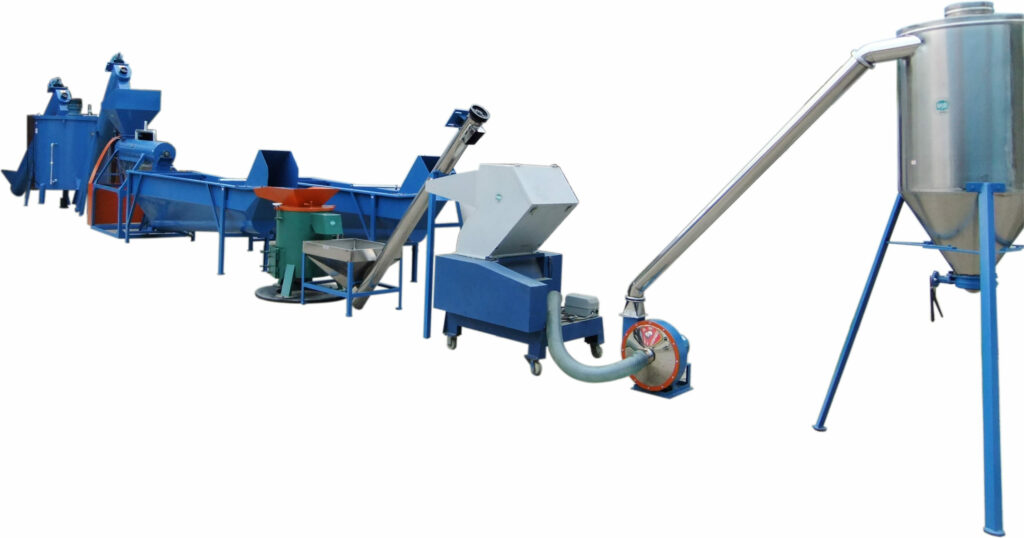
Injection molding process
Feeding-plasticizing-injection-holding pressure-cooling-opening mold
Plastic molding is the key to plastics processing. There are more than thirty methods for molding, mainly plastics (powder, granules, solutions or dispersions) of various forms that are made into products or blanks of desired shapes.
The molding method is mainly determined by the type of plastic (thermoplastic or thermosetting), the initial form, the shape and size of the product. Common methods for processing thermoplastics include extrusion, injection molding, calendaring, blow molding, and thermoforming. Processing thermosetting plastics generally uses compression molding, transfer molding, and injection molding. Laminating, molding, and thermoforming are molding plastics on a flat surface.
The post-processing of the plastic.
The post-processing of plastic parts includes the modification of the production surface of plastic products. The purpose of this step is to beautify the surface of the plastic product and usually includes:
Mechanical modification, that is, using files, grinding, polishing and other processes to remove burrs on parts and correct dimensions;
Finishing, including coating the surface of the product with paint, brightening the surface with a solvent, and covering the surface of the product with a patterned film;
Applying color, including painting, printing, and hot stamping; metal plating, including vacuum coating, electroplating, and chemical silver plating.
Plastic processing hot stamping is to transfer the colored aluminum foil layer (or other pattern film layer) on the hot stamping film to the product under heat and pressure. Many household appliances, construction products, daily necessities, etc. use this method to obtain patterns such as metallic luster or wood grain.
In fact, the last step is to recycle the used plastic. We have a professional plastic recycling production line to achieve the purpose of this step.